Why Your Maintenance Plan Might Be Failing: Insights from SeaLogs
- Hannah M
- Apr 11, 2024
- 6 min read
Updated: Apr 16, 2024
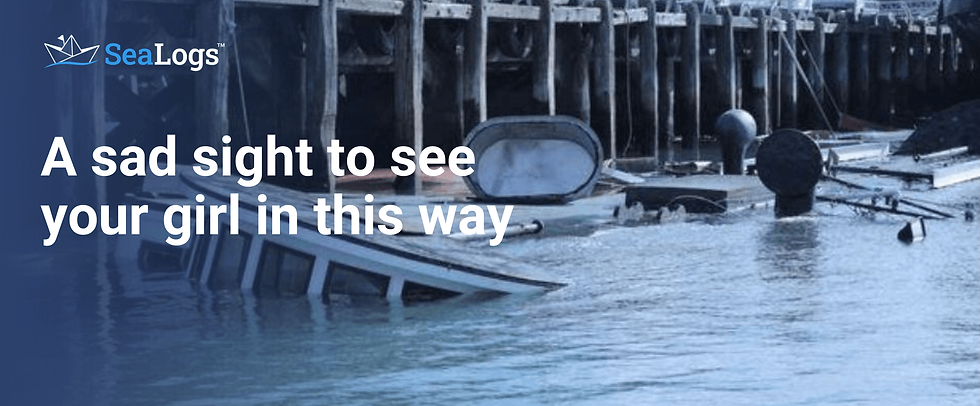
Long story short: The definition of a boat is a hole in the water you pour money into. Simply put, if do not have the money, time, or ability to do proper maintenance, get out of the game, because it is only a matter of time before you kill yourself or even worse; kill someone else. Boats, irrelevant of their size, need continuous maintenance.

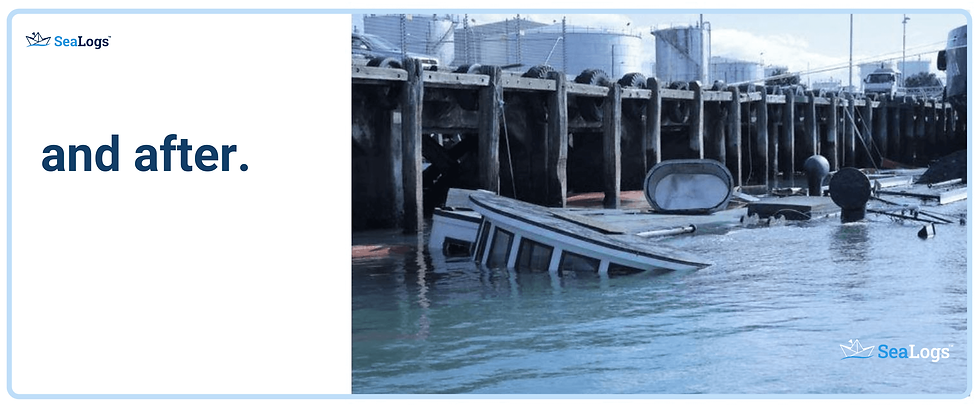
There is always something to be done on a boat, that is just the nature of the game. There is however, a trick to it all; do these tasks in a logical and organised manner. Most vessels run more than one crew, and here it is imperative that effective communication between the various crews is carried out. “SeaLogs” provides an effective way to ensure this happens. The maintenance can be tailored to each individual vessel or to a fleet, and can also be monitored by onshore operational staff. Skippers and engineers can walk off a vessel knowing that the on-coming crew know exactly what has been done: the state of all the equipment onboard the vessel, fluid levels, and upcoming maintenance schedules. This is where the keeping of records is essential.
Where to start? First, the vessel must be cleaned and pristine, the bilges clean, the engine as clean as possible, rubbish off the vessel, and decks squared away of loose equipment, ropes, and other wayward items. I am not kidding; clean the boat up! It does not matter whether it was your fault or not, your mess or someone else's. You are the one taking the vessel out to sea. I judge a vessel on first appearances and if the crew or owners cannot be bothered keeping the vessel clean, then I seriously would question their ability to run that vessel safely.
Typical factory, spotless.
There is somewhere between 30 to 60 tonnes of equipment spread around this deck, all correctly stowed and secured. If we can do it on fishing vessels there is no excuse for it not to be done on any vessel.
Once the vessel is as clean and tidy as possible, sit down and make a plan. I have been told over and over that a good rule of thumb is to spend around 10% of the value of the vessel on maintenance each year. As the vessel gets older, you will need to spend increasingly more until it reaches a point where it becomes uneconomic, irrespective of whether it is a recreational or commercial vessel. Again, here is where a system like “SeaLogs” will aid you immensely. You can begin to list all the vital equipment, maintenance and other vessel specific schedules that need to be carried out. “SeaLogs” also has an industry standard schedule for the maintenance of these items, such as for commercial survey.
I am not an engineer, not by any stretch of the imagination, so first and foremost know your limitations. I can drive a boat, catch fish, and do all the other seamanship things that make for a safe passage but you are a fool if you expect me to do an oil change. I can guarantee to stuff it up and it will end up costing much more. People say, “it’s easy,” well, I have seen and been on vessels that have experienced everything from engine failures, bilge pump failures, total electrical failures, and so on, all of which have cost the company anything from hundreds to millions of dollars because someone did not know what they were doing!
For example:
“One of our vessels is in dry-dock. The company takes the opportunity to refurbish the winches at the same time. The contractors approached the company and clearly stated that they were not happy doing this particular job, but they were brow-beaten into doing the work by senior management. One week into the first trip post dry-dock, the vessel in question knew they had a problem. The winches were misbehaving, making a terrible noise, so the vessel headed back to port. Now began a six-month saga, because the contractors had installed the vanes in the winches around the wrong way. Every hydraulic pipe had to be taken off the vessel, cleaned and replaced, all the hydraulic tanks had to be drained and then the complete system had to bled and checked. $6 Million dollars later plus another 18 months wrangling with the insurance company's arguing over who should pay the bill, six months of no fish, having to re-build a completely new crew, wharf fees and on and on. Getting the right contractors in from the start seemed so simple!”
These are the types of stories you do not hear about because companies like to keep them quiet. But in reality, these are the stories you should know about. It is not like anyone was incompetent, the contractors were one of NZ’s leading engineering firms. The company in question and the managers are competent, capable managers any firm would be proud to have but they just pushed their luck a bit much. I know for sure they have made countless good decisions over time, but a few bad calls like this can ruin a career.
When I sit down and look at maintenance, I look at the following points.
Essential jobs, survey requirements and lifesaving equipment; radios, GPS’s etc. You do not have a choice with this stuff, it must be done, by law, end of story.
Engine room and machinery. I like to get there and back without having to offer sacrifices to the gods. This needs to be done in conjunction with your budget, all gear wears out eventually, irrespective of the vessel. I have found the best results come from those that have a realistic view regarding engine and equipment replacement. Boats do not make much money tied up alongside the wharf. Often there is a large element of false economy; where by the time the vessel has broken down half a dozen times, been towed back, repaired repeatedly, it would have been cheaper to have bitten the bullet in the first place and replaced the offending piece of machinery. Sorry, boats cost money, get used to it.
Painting, antifouling, and dry-docking/slipping. For larger vessels this has become a real nightmare, there are not enough dry docks around NZ and often companies will just have to program dry-docking when they can get a slot. For most other operators, slipping and cosmetics can be scheduled to fit in with seasonal operations.
These vessels only get dry-docked once every three years, it is expensive to do, but savings in fuel will more than cover the costs over periods between dockings.
At the end of the day, how you maintain your vessel will reflect on you as a person and your business. It shows that you care about your vessel, your crew and especially your customers. I like to be organised about maintenance, from greasing schedules to major refits, because all too often it is a case of a ‘stich in time saves nine.’
“SeaLogs” will simplify this decision-making process for you and here I will repeat myself. Sit down and get organised; work out what needs to done, when it needs to be done, who will do it and how often. This will make your life a lot easier, and you can get on and do the things you want to do. Whether that is just running around the Briney or effectively running your vessel or business to its true potential. There is an old saying, “work on your business, not at it”.
Have a look at these two vessels,’ there are tonnes and tonnes of gear going onto these two vessels, yet they are tidy and well-organised. They will both spend over 100 days in the Antarctic and this is where vessel maintenance will be tested to the limit. But it starts here on the wharf, with things like rubbish skips, chemical toilets, safety nets below gangways, crew wearing hard hats, clean overalls, and steel-capped boots. These are all costs that need to be accounted for when doing maintenance because the penalties for a failure at any stage will not only blow out budgets but could impose horrific fines and restrictions. These vessels reflect just how much the fishing industry in NZ has changed over the last thirty years to where NZ now leads the world. Nothing happens by accident, but by learning from past mistakes and ensuring they do not happen again. Organisation, pre-planning, and a realistic pragmatic attitude has lifted this industry into the 21st century.
Take care out there everyone and all the best.
- Captain M. Prendeville